1. Technical introduction.
CNC machining usually refers to precision machining controlled by computer digitally, also known as NC machining, which refers to the processing carried out with NC machining tools. Because NC machining is controlled by computer after programming, CNC machining has the advantages of stable machining quality, high machining precision, high repetitive precision, machinable complex surfaces, high machining efficiency and so on.
2.Process flow.
(1) read drawings and program lists.
(2) transfer the corresponding program to the machine tool.
(3) check program head, cutting parameters, etc.
(4) determination of machining size and margin on the workpiece.
(5) reasonable clamping of workpiece.
(6) accurate alignment of workpiece.
(7) accurate establishment of workpiece coordinates.
(8) selection of reasonable cutting tools and cutting parameters.
(9) reasonable clamping of cutting tools.
(10) safe trial cutting.
(11) observation of machining process.
(12) Adjustment of cutting parameters.
(13) problems in the machining process and timely feedback from corresponding personnel.
(14) Inspection of workpiece quality after machining.
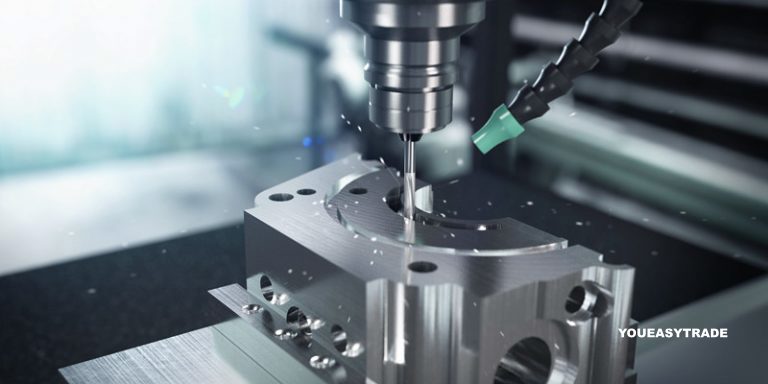
3.Common problems in CNC processing and how to solve them.
1). Workpiece overcutting.
Reason:
(1) bullet knife, the strength of the tool is not too long or too small, resulting in the knife.
(2) improper operation of the operator.
(3) uneven cutting allowance (for example, 0.5 on the side of the surface and 0.15 on the bottom).
(4) improper cutting parameters (such as too large tolerance, too fast SF setting, etc.).
Improvement:
(1) the principle of using a knife: it can be too small, short or not.
(2) add the corner clearing program and leave the margin as uniform as possible (the margin of the side is the same as that of the bottom).
(3) adjust the cutting parameters reasonably and fix the circle at the corner with large margin.
(4) using the SF function of the machine tool, the operator can fine-tune the speed to achieve the best effect of machine tool cutting.
2).Split-center problem.
Reason:
(1) the operator is not accurate in manual operation.
(2) there are burrs around the mold.
(3) the split rod is magnetic.
(4) the four sides of the mold are not vertical.
Improvement:
(1) the manual operation should be checked repeatedly and carefully, at the same point and at the same height as far as possible.
(2) the periphery of the mold is deburred with oilstone or file, then cleaned with rags, and finally confirmed by hand.
(3) demagnetization of the split rod before dividing the mold (ceramic bar or other can be used).
(4) check the meter to check whether the four sides of the mold are vertical (the verticality error needs to be reviewed with the fitter).
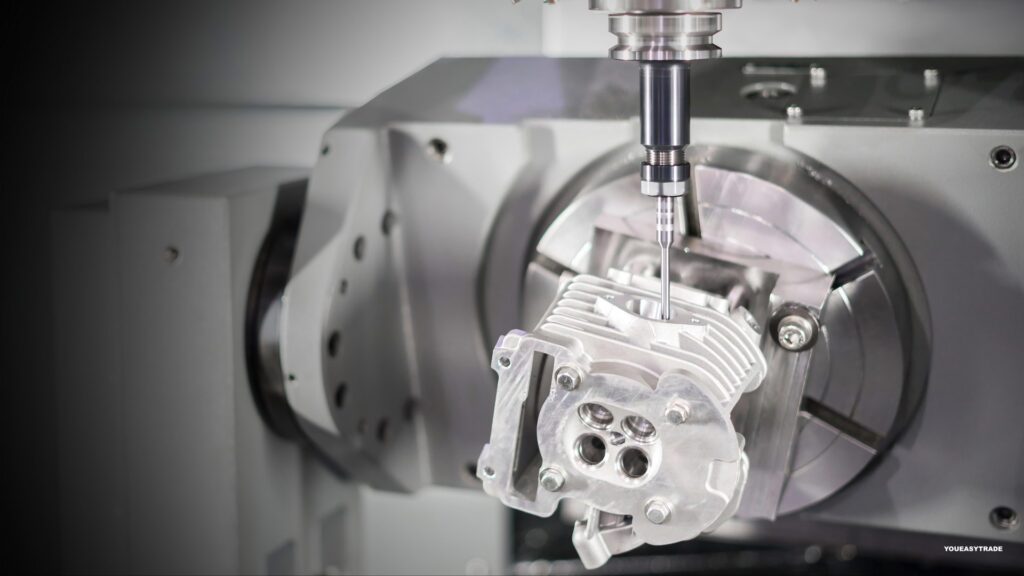
4. Collision programming.
Reason:
(1) the safety height is not enough or not set (the knife or chuck hits the workpiece when fast feeding G00).
(2) the tool on the program list and the actual program tool are miswritten.
(3) the tool length (edge length) on the program sheet and the depth of the actual processing are miswritten.
(4) the number of deep Z-axis and the number of actual Z-axis on the program sheet are miswritten.
(5) the coordinate setting is wrong when programming.
Improvement:
(1) accurately measure the height of the workpiece to ensure that the safe height is above the workpiece.
(2) the tool on the program list should be consistent with the actual program tool (using automatic program order or picture program sheet as far as possible).
(3) measure the actual depth of machining on the workpiece, and write clearly the tool length and edge length on the program sheet (generally the tool clip length is 2-3MM higher than the workpiece, and the blade length is 0.5-1.0MM).
(4) take the actual Z-axis number on the workpiece and write it clearly on the program list. (this operation is usually done manually and checked over and over again.).
5.Surface precision.
Reason:
(1) the cutting parameters are unreasonable and the surface of the workpiece is rough.
(2) the edge of the tool is not sharp.
(3) the clamping of the tool is too long and the blade avoids the void for too long.
(4) it is not good to discharge chips, blow air and flush oil.
(5) programming knife-walking mode, (you can consider walking and milling as far as possible).
(6) the workpiece has burr.
Improvement:
(1) the setting of cutting parameters, tolerance, allowance and rotational speed feed should be reasonable.
(2) the cutter requires the operator to check and replace it from time to time.
(3) when clamping the tool, the operator is required to clamp as short as possible, and the blade should not be too long.
(4) for the undercutting of flat knife, R knife and round nose knife, the rotational speed feed setting should be reasonable.
(5) the burr of the workpiece is directly related to our machine tools, cutting tools and cutting methods. So we need to understand the performance of the machine tool and mend the burr edge.